Maria Huffman, director of the Washington Nanofabrication Facility (WNF), has stepped down to take on new challenges as the director of the Swedish Chips Competence Center (SCCC). Darick Baker, who has served as the engineering and business development manager, has been named acting director.
WNF announces acting director following Maria Huffman departure
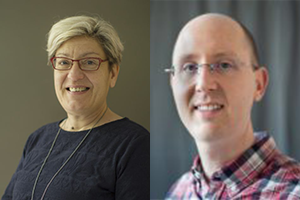